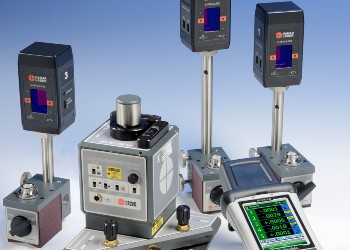
L-743 Ultra-Precision Triple Scan® Laser Alignment System
MACHINE TOOL LEVELING & ALIGNMENT
Machine leveling is a broad term used in the machine tool industry during machine installation of machine tables, rails, and the base. While it is critical in some applications that the machine base, rails, and tables are level, it is more important that machine axes, spindle, and the working surfaces have excellent geometric relationships per the machine’s intended design. Machine alignment is the term Gnex Engineering uses when installing and adjusting machinery so that the moving axes produce accurate motion profiles at the tool tip. Achieving excellent machine geometry between machine axes requires measurements of straightness and angular errors of each axis, and then measurements are made to understand the orientation of the axes to each other. This process is considered as a baseline geometry characterization of the machine tool. The data from this characterization event is very detailed and allows us to develop the best approach to establish excellent machine geometry because Gnex Engineering is able to consider the overall picture as well as isolated areas that require improvement. This approach allows Gnex Engineering to focus efforts aligning the critical areas that have the greatest effect on machine geometric performance versus time and effort on areas that will have achieved little to no gain in machine performance.MACHINE ALIGNMENT SERVICES
Machine accuracy and repeatability are necessary for a machine to perform to its full capabilities and proper machine alignments are fundamental for this to happen. Machine leveling should be performed periodically to ensure the machine is in good tolerance, after a relocation or incorrect installation, after a machine repair or “crash”, or to recertify the machine. Gnex Engineering recommends that machine adjustments be a part of regular occurring preventive maintenance program to help extend the life of your machine tool. Gnex Engineering has aligned machines of all types and sizes from machining centers to long bed gantries.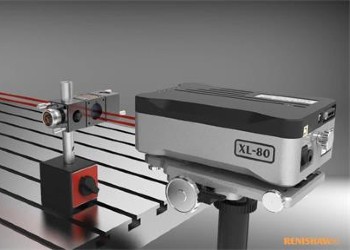
Renishaw Laser Interferometer XL-80
ACCURACY AND PRECISION ARE IMPORTANT.
ACCURACY AND PRECISION ARE IMPORTANT.
We can help your business save money and time by making sure you get the right cut the first time. We uses Renishaw XL 80 laser system to calibrate the linear accuracy of all types of machines. The XL 80 laser produces an extremely stable laser beam, for dynamic performance. All measurement options are based on interferometric measurements, giving confidence in the accuracy of data recorded. This is a fast way of qualifying and correcting positional accuracy on equipment.
Every linear calibration will come with a detailed report outlining the machine’s condition and the final results post calibration. We recommend that machines are checked for linear accuracy annually in order to maintain your performance.
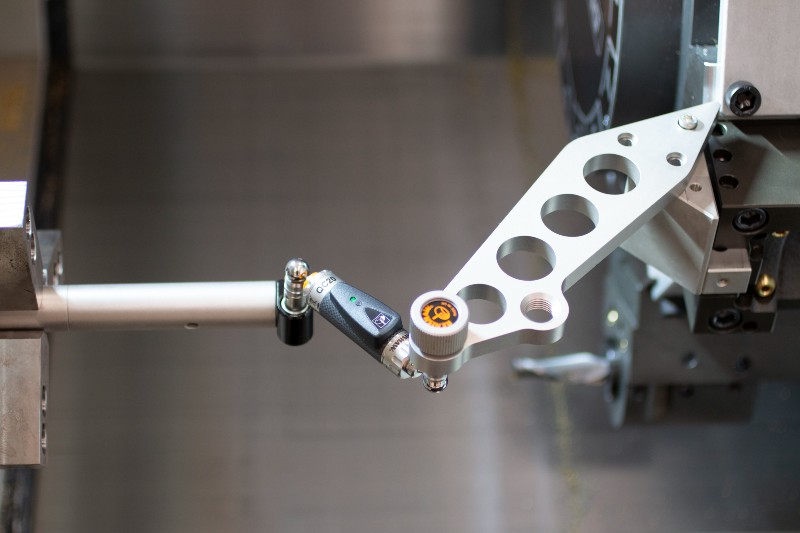
Renishaw QC20-W ballbar system. (Dynamic Ballbar Calibration)
We use the Renishaw QC20-W wireless ball bar system for dynamic machine tool performance diagnosis. The ball bar has a system accuracy of +/- 1.25µm and can be set to calibration from 100 to 600mm radii.
We also have the small circle kit with a 50mm radii test, Lathe adapter to perform checks for Lathe & VTL.
Tests are performed in both clockwise and counterclockwise directions to evaluate error. Additionally, we can provide partial arc testing up to 220 degrees throughout the center pivot axis point.
The results are displayed with definitions and possible causes. Reports are generated and can be formatted for the following standards. ISO 230-4, ASME B5.54 and ASME B5.57
Regular ballbar testing of machine tools helps to:
- Ensure accurate parts, first time, from CNC machines reduce machine down-time, scrap and inspection costs
- Demonstrate compliance with machine performance and quality management standards
- implement fact based predictive maintenance
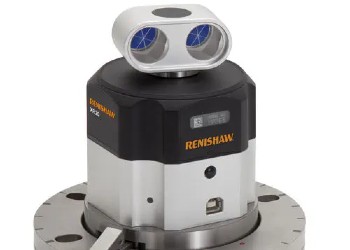
Rotary AXIS Calibrater XR 20-W
When XL 80 is used in conjunction with the XR2-W Rotary Axis calibrator we are able to 0ffer both A and B axis rotary calibration. The XR20-W system allows us to measure rotational axis position to within 1 arc second.
We also provide services to measure and correct “center of rotation” errors for 4 and 5 axis systems.
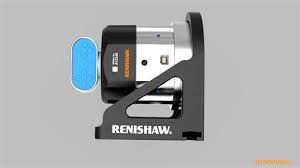
XR20 90° Bracket
We also provide services to measure and correct “center of rotation” errors for 4 and 5 axis systems with XR20 90° bracket.
Flexible fixturing options are provided by removable magnetic feet and a variety of through holes for direct bolt attachment. The bracket is useful for meeting the mounting requirements of ‘off-axis’ rotary measurements and resolving ‘on-axis’ mounting difficulties on trunion type machines.